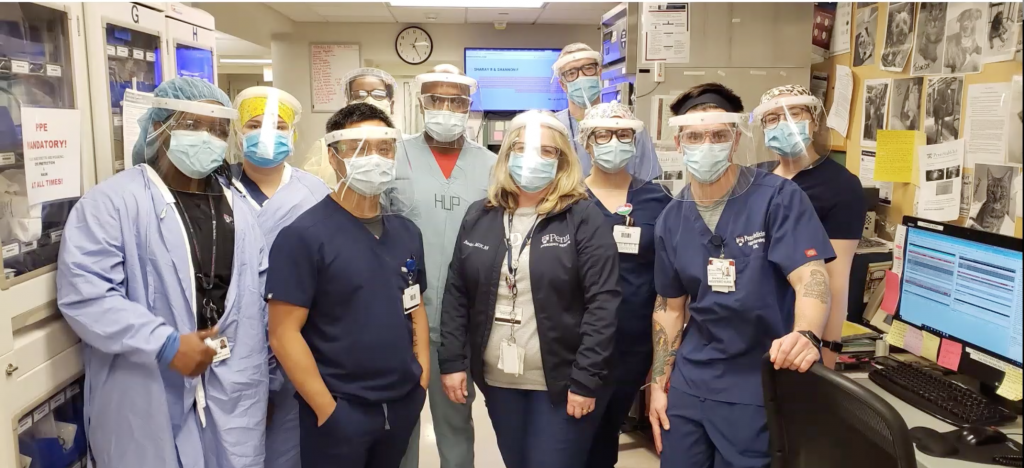
Every year, Penn Health Tech (PHT) hosts a call for proposals that center the organization’s ethos: developing solutions that merge the fields of medicine and engineering.
This year, with the ethos still in the foreground, the specific goals changed.
“In response to the COVID-19 pandemic, we rapidly pivoted to create an initiative that we call the Rapid Response Teams,” said Victoria Berenholz, Executive Director of PHT.
Berenholz, together with Brian Litt, Dr. David Meaney and Dr. Kevin Turner, quickly assumed leadership roles.
Each of the 7 teams of the initiative focused on a specific need that included face shields, telemedicine carts, intubation PPE, and emergency ventilators.
Neil Ray, an ER doctor at HUP who worked with the initiative, felt the pressure early in the pandemic’s insurgence.
“It was a very scary time…we didn’t know much about how it was transmitted,” said Ray. “We needed face shields and we needed masks, we just didn’t have the resources to get them.”
Mark Yim – Professor of Mechanical Engineering, and Director of the GRASP (General Robotics, Automation, Sensing and Perception) Lab – opted to be a part of the face shield team. Although the need for shields was dire, hospital protocol was constantly changing requirements. Designs should not be too close to the face (so as not to cause fogging), they should be secure and comfortable, and they should be reusable.
A shortage of suitable materials such as PETG, PET, and cellulose acetate meant they might have to get particularly resourceful. Consequently, vendor delays and other hiccups threatened an already tight timeline. The urgency of the situation was ever looming.
“We were thinking we might need to get soda bottles and cut them up,” said Yim. “Clear plastic was why most of the vendors were having problems with [producing] face shields.”
The team didn’t need to resort to recycling bin raids to secure materials, and the process moved forward into production, marked by 3 phases: 1) design and prototype, 2) 3D/foam production and 3) riveted production. The second and third phases followed the team’s progression from their first 2 design types: foam (the easiest to make) and 3D printed, to the riveted. Hospitals’ preferences for the riveted model, in addition to it being easier to construct than the foam, contributed to the production of roughly 10,000 riveted models alone.
At the Pennovation Center, CIS staff member Charity Payne — Associate Director of both the GRASP Lab and PERCH (Penn Engineering Research and Collaboration Hub) — led a team of volunteer students responsible for shield and short band attachment. Afterwards, they were sent to Gaby Alvaro (GRASP Lab) and her team in the Levine Lobby for long band attachment and final assembly. Together they helped contribute to the creation of 1000-2000 shields per day.
“As a result of you guys’ hard work, we’ve had face shields, not only in the emergency department, but in the ICUs, and every floor, “ said ER doctor Ray in a virtual recap meeting. “You were actively impacting patient care, in a time when we needed you guys the most. “
Overall, the initiative was responsible for the production and delivery of over 15,000 shields to 5 Penn Medicine hospitals: Chester, HUP (5,000), Pennsylvania, Presbyterian and Princeton. Roughly 200-300 volunteers came together to make this happen, most of which hustled into formation to finish assembly of the riveted models at the end of phase 3.
Despite these impactful results, PHT’s ED knows there is still more work to be done.
“[We] continue to source opportunities for new projects,” said Berenholz. “Even as we move out of this acute crisis phase.”
** Click here to submit proposals for the Rapid Response Teams **
** Click here for more in-depth coverage **